As industries go, residential construction in America has largely weathered the pandemic thanks to steady demand and low interest rates. Worksites nationwide are humming with good, paying jobs at a time when 1 in 8 workers are receiving unemployment checks. So why on earth are some construction firms complaining of a labor shortage?
U.S. construction is sprawling, employing roughly 5% of the nation’s workforce (7.3 million employees) at some 680,000 firms, according to the Bureau of Labor Statistics (BLS). The industry is essentially its own economy, building hundreds of billions of dollars worth of structures each month. It’s true that many parts of the sector are hurting because of the pandemic. But in others, there’s actually too much work to go around.
A survey by the National Association of Home Builders (NAHB) found that builders’ top concern is labor, with 85% expecting future cost and availability problems, up from 13% in 2011. It’s a conundrum that predates the pandemic, but one that’s certainly been exacerbated by it.
While unemployment peaked at almost 15% in 2020, empty construction jobs nevertheless hovered between 223,000 and 332,000—about the same number of open slots back when unemployment was only 4.1%. So what gives?
“You’ve got a lot of folks who are recently unemployed, but still don’t think of construction careers as an opportunity,” said Brian Turmail, vice president of strategic initiatives and public affairs at Associated General Contractors of America (AGC), which in the spring plans a nationwide recruiting campaign called “Construction is Essential.”
“There’s an impression that construction careers are like a job of last resort, and not a rewarding kind of middle-class career,” he said. “Yet in many respects, they are a lot more rewarding than sitting in some kind of fluorescent-lit cube farm.”
But if you are one of those unemployed Americans willing to try, be forewarned: entry level construction workers are not what many firms are looking for. You have to know what you’re doing.
Daniel Lane, vice president and installation manager at Flint, Michigan-based American Metal Roofs, said he tried to fill 10 positions last year for seven residential roofing crews throughout Michigan. It took him more than 6 months—despite paying his employees bounties for bringing in successful new hires. “A third of our applicants can’t read the tape measure,” he said.
Pre-pandemic, the industry was already partnering with correctional facilities to find day workers to keep projects moving. Now, wage-wars have erupted, inflating starting rates, Lane said.
“We’re all fighting for that same guy—in our region, at $18-an-hour plus paid-travel time, you’re not going to get anybody replying to your ads but entry level.” (The demand for construction, however, is not being felt when it comes to infrastructure projects.)
Read More: ‘Recovery? What Recovery?’ Ask Bridge Builders, Tractor Makers
This is the secret about construction that many people don’t get: positions that typically pay good money require technical knowledge and significant training, while others can mandate certifications and college degrees. Add to that common misperceptions that keep many people from considering construction work in the first place, and you have the recipe for a labor shortfall.
Such hiring lags have become a huge headache for some developers. “I’m looking to reduce all of my construction costs, and I see the prices of everything are going down, but the labor is not,” said Eran Polack, chief executive of HAP Investments, which had seven projects underway in New York City. “There was a 16% unemployment rate in New York, so I’m asking…everybody, ‘how come you can’t reduce the cost?’”
cost?’”
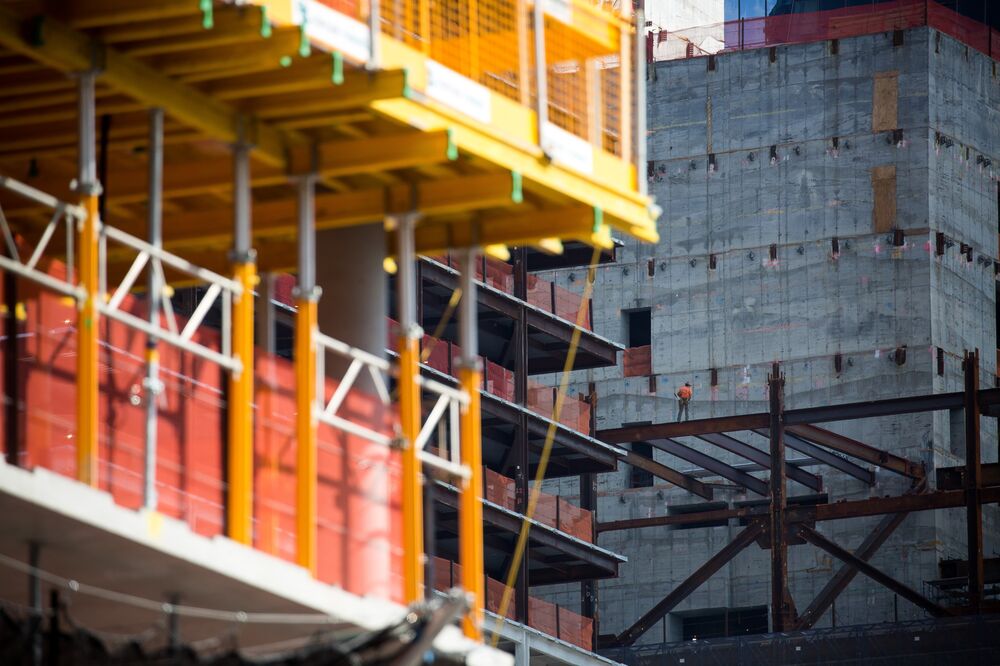
In 2019, construction careers paid laborers on average $42,320 a year; carpenters took home $53,150, while managers earned $103,960, according to the BLS. Certifications differ for trades like electricians and plumbers, as well as for types of construction such as residential, commercial and industrial. Training time varies from 4-week introductory courses to two-year trade school certificates.
It’s this required training—both the expense and unavailability—that may be deepening the labor problem.
“When you say 300,000 available jobs, they’re not all skilled labor—but many of them are,” said Ed Brady, president and CEO of the Home Builders Institute, a non-profit training program associated with the NAHB. “For 20 years, we haven’t trained and spent money on educating, and at the same time a lot of the industry is retiring. So the skills gap is going to get worse before it gets better.”
Who should be subsidizing this training is a topic of much finger-pointing, given the increasingly expensive, state-of-the-art equipment required to learn some trades. Developers point at trade schools and industry organizations; trade schools and industry groups want government dollars; job seekers look to employers. Thanks to the coronavirus, many schools are struggling while others have closed their doors—making it harder for students to get the skills they need.
“It takes funding, it takes legislative support, it takes community support,” Brady said. “If we had more funding, we could train more people.”
Nathan Barry, dean of career and technical education at Metropolitan Community College in Omaha, Nebraska, said instructor salaries need a boost, too. His 1,000-student education center offers courses ranging from civil engineering and architecture to electrical welding and construction management. Some trade-school faculty can easily make six figures working in construction rather than teaching, Barry explained.
With commercial construction stagnant, apprenticeship programs at construction companies are largely on ice, adding to the labor problem. “Our message to our members is that we understand the reasons you do that,” said Turmail of the AGC, “but that may not be the most far-sighted policy.”
Some students currently in trade-school programs have been forced by Covid-19 to learn wiring and construction management over video conference, practicing on mailed-out electrical kits and watching through site managers’ GoPro cameras. (Additionally, numerous high school trade programs have shuttered altogether.)
“We’re actually in a kind of workforce development crisis, or calamity, because so many folks who would otherwise be learning construction crafts aren’t, because you just can’t do it via Teams or Zoom,” says Turmail. “The education pipeline, which was never great to begin with, is drying up.”
“We’ve done a terrible job of branding to parents.”
As retirement beckons to a sizable percentage of the U.S. construction workforce, Brady said the labor shortage will worsen.
“You’re retiring a 30-year carpenter and replacing him with someone two years in, who can’t do it as fast and can’t do it with the same quality,” he said. “The industry pays very well, but it pays according to skill, pace and production, and it’s harder to get a job if you have no involvement through training and certification.”
“We’ve done a terrible job of branding to parents,” Barry said. “Imagine a 15-year-old telling mom and dad, ‘Well, I think I want to be a plumber.’ Mom and dad are going to say, ‘Not that there’s anything wrong with that, but let’s have higher aspirations.’” Meanwhile, some 70% of plumbing is new construction and starting plumbers make $50,000-60,000 a year—using cameras and an iPad to do much of the work.
“The kid knows this,” Barry said. “The parents don’t.”