The many, many benefits of using wood in place of concrete and steel.
Architects, builders, and sustainability advocates are all abuzz over a new building material they say could substantially reduce greenhouse gas (GHG) emissions in the building sector, slash the waste, pollution, and costs associated with construction, and create a more physically, psychologically, and aesthetically healthy built environment.
The material is known as, uh, wood.
Trees have been used to build structures since prehistory, but especially after disasters like the Great Chicago Fire of 1871, wood came to be seen as unsafe and unstable relative to the two materials that have since become staples of the construction industry worldwide: concrete and steel.
However, a new way of using wood has put the material back in the spotlight. The hype is focused on structural timber or, as it’s more popularly known, “mass timber” (short for “massive timber”). In a nutshell, it involves sticking pieces of soft wood — generally conifers like pine, spruce, or fir, but also sometimes deciduous species such as birch, ash, and beech — together to form larger pieces.
Yes, the hottest thing in architecture this century amounts to “wood, but like Legos.”
Mass timber is a generic term that encompasses products of various sizes and functions, like glue-laminated (glulam) beams, laminated veneer lumber (LVL), nail-laminated timber (NLT), and dowel-laminated timber (DLT). But the most common and most familiar form of mass timber, the one that has opened up the most new architectural possibilities, is cross-laminated timber (CLT).
To create CLT, lumber boards that have been trimmed and kiln-dried are glued atop one another in layers, crosswise, with the grain of each layer facing against the grain of the layer adjacent. Stacking boards together this way can create large slabs, up to a foot thick and as large as 18-feet-long by 98-feet-wide, though the average is something more like 10 by 40. (At this point, the size of slabs is restricted less by manufacturing limitations than by transportation limitations.)
Slabs of wood this large can match or exceed the performance of concrete and steel. CLT can be used to make floors, walls, ceilings — entire buildings. The world’s tallest mass timber structure, at 18 stories and over 280 feet, was recently built in Norway; there’s an 80-story wooden tower proposed for Chicago.
I talked to lots of people who are extremely excited about mass timber, both for its architectural qualities and for its potential to help decarbonize the building sector, and a few raised important cautions. We’ll run through all the advantages and caveats in a moment. But first, let’s take a quick spin through the history of mass timber and where it currently stands.
CLT was first developed in the early 1990s in Austria, where softwood forestry is extremely common. It was championed by researcher Gerhard Schickhofer, who is still active and who won a prestigious forestry prize last year for his work to standardize and secure popular support for the new material.
In Austria and in Europe generally, where it spread in the 2000s, CLT was developed for use in residential construction. Europeans do not like the flimsy wood stick-frame construction used for so many US houses; they prefer more solid materials like concrete or brick. CLT was meant to make residential construction more sustainable.
But in the US, CLT can’t (yet) compete with stick-frame construction, which is cheap and ubiquitous. It wasn’t until North American architects got the idea of using CLT in bigger buildings, as a substitute for concrete and steel, that it began popping up in North America in the 2010s.
In 2015, CLT was incorporated into the International Building Code (IBC), which jurisdictions across the US adopt as their default. A set of new changes that will enable mass timber structures up to 18 stories tall have been accepted and are expected to be formalized into the newest IBC code in 2021.
Some jurisdictions in the US have been aggressive about supporting mass timber, including Washington and Oregon (which have preemptively accepted the new changes to the IBC; Oregon incorporated CLT as a “statewide alternative method” in 2018).
The Pacific Northwest is understandably excited about a possible shift to wooden building materials, as it is home to copious forests and idled sawmills.
“Timber harvest in [the Pacific Northwest] has declined significantly as a result of the weak domestic demand during the housing crisis, which has been devastating to the forest products industry,” reports a recent study of CLT lifecycle emissions. “In Washington State, the volume of lumber produced declined 17% between 2014 and 2016 and, compared to 10 years ago, lumber mills (the largest sector by timber consumption) produced one third fewer boards.”
Nationally, forests are so overstocked that the Forestry Department is giving out $9 million in grants for new ideas for how to use wood. Plenty of local communities would welcome new demand.
While CLT is continuing to explode in Europe and is accelerating in Canada, it remains hampered in the US by anachronistic and overly prescriptive building codes, limited domestic supply, and the small-c conservative thinking of the building trades.
On the supply front, Vaagen Brothers, a well-known Washington sawmill, has already retooled around CLT; other mills are expected to follow. A company called Katerra recently opened the largest CLT manufacturing facility in North America in Spokane, Washington, with state lawmakers on hand to celebrate. That may help mass timber get going in earnest in the region.
Governor Jay Inslee
✔
@GovInslee
Our state leads in so many ways, and now Washington will lead the nation in manufacturing cross-laminated timber for buildings with the new @katerrainc facility in Spokane. https://medium.com/wagovernor/engineered-wood-product-industry-helps-lower-carbon-emissions-and-create-jobs-8a92517f82ef …
Engineered wood product industry helps lower carbon emissions and create jobs
Gov. Jay Inslee joined state leaders to celebrate a mass timber manufacturing facility in Spokane Friday that could usher in a new chapter…
For now, there are a number of flashy one-off CLT projects in the US: the Catalyst innovation hub in Spokane, the T3 office building in Minneapolis, the Carbon 12 condominiums in Portland, Oregon, Franklin Elementary School in West Virginia, and more. But because they are one-offs, they require a lot of extra work in testing, designing, and securing permits. And there’s a shortage of both suitable materials and contractors and builders familiar with them. “It’s not a mature industry,” says architect Michael Green, whose seminal 2013 TED Talk on mass timber helped kickstart interest in the US. (Side note: Katerra recently acquired Michael Green Architecture.)
Nonetheless, the growing enthusiasm of builders and advocates seems to be chipping away at the resistance. Why are they so geared up?
The advantages of mass timber
1. It performs well in fire
Especially in the US, people associate wood in buildings with stick-frame construction, 2X4s and plywood, which are flammable AF. It doesn’t help that the media has recently been full of images of stick-frame houses and subdivisions burning in California. It is everyone’s first question about mass timber: what about fire?
The thing is, large, solid, compressed masses of wood are actually quite difficult to ignite. (Hold a match up to a large log some time.) In the case of fire, the outer layer of mass timber will tend to char in a predictable way that effectively self-extinguishes and shields the interior, allowing it to retain structural integrity for several hours in even intense fire.
Reports on fire testing of CLT come from the US Forest Service, the International Code Council, and the Fire Protection Research Foundation. (The Forest Service has also done extensive blast testing of CLT, which it passed with flying colors, opening the door to its use in military facilities.) The bottom line is that all building materials have to meet code, and CLT meets code for fire safety.
An interesting aside: Most people don’t realize that “steel is terrible in fire,” says Green. “Once it reaches a yielding temperature, it becomes highly unpredictable, and it’s done. Your building has to be torn down.” When Green does use steel, he often surrounds it with CLT to protect it in the event of fire.
2. It reduces carbon emissions
Roughly 11 percent of global greenhouse gas emissions come from building materials and construction; another 28 percent comes from building operations, which mostly involve energy. As energy gets cleaner in coming years, materials and construction will represent a growing fraction of buildings’ carbon impact. That’s what mass timber aims to reduce.
Determining the full lifecycle impact of mass timber on carbon emissions is a tricky business. At least three carbon effects must be tallied up.
First, some greenhouse gas emissions are released by the supply chain, starting with forestry. In logging, soil carbon is disturbed and released, plant and wood waste is generated that eventually rots and releases carbon, and emissions are generated by the vehicles and machinery necessary to cut the wood, transport it to the mill, and treat it. Notably, most conventional lifecycle analysis counts wood supply as carbon-neutral, assuming it comes from sustainably managed forests; as we will see later, that’s not always a safe assumption.
Second, there is some amount of carbon embedded in the timber itself, where it is sequestered in buildings that could last anywhere from 50 to hundreds of years. Though the exact amount will depend on tree species, forestry practices, transportation costs, and a number of other factors, Green says a good rule of thumb (confirmed by this study) is that one cubic meter of CLT wood sequesters roughly one tonne (1.1 US tons) of CO2.
(Again, as we’ll see later, this depends on some assumptions about forestry.)
Third and most significantly, substituting mass timber for concrete and steel avoids the carbon embedded in those materials, which is substantial. Cement and concrete manufacture are responsible for around 8 percent of global GHG emissions, more than any country save the US and China. The global iron and steel industry is responsible for another 5 percent. Something like half a ton of CO2 is emitted to manufacture a ton of concrete; 2 tons of CO2 are emitted in the manufacture of a ton of steel. All those embodied emissions are avoided when CLT is substituted.
Exactly how those three carbon effects balance out will depend on individual cases, but research suggests that, for all but the most poorly managed forests, the overall impact of using CLT in place of concrete and steel will be a reduction in GHGs. A 2014 study in the Journal of Sustainable Forestry looked deep into the question of the carbon effects of large-scale substitution of wood products for alternatives and concluded: “Globally, both enough extra wood can be harvested sustainably and enough infrastructure of buildings and bridges needs to be built to reduce annual CO2 emissions by 14 to 31% and FF consumption by 12 to 19% if part of this infrastructure were made of wood.” The biggest drop in CO2 emissions came, it said, from “avoiding the excess [fossil fuel] energy used to make steel and concrete structures.”
More recently, a team at the University of Washington attempted a full, soup-to-nuts lifecycle analysis comparing a “hybrid, mid-rise, cross-laminated timber (CLT) commercial building” to “a reinforced concrete building with similar functional characteristics.” After tallying up all the many factors, they concluded that the CLT building represented a “26.5% reduction in global warming potential.”
That’s likely a decent rule-of-thumb estimate, though again, that number could be pushed in either direction by better or worse forestry, transportation, milling, construction, and disposal practices.
3. It allows buildings to be constructed faster, with lower labor costs and less waste
Rather than materials being ordered in mass quantities, cut to size on site, and assembled, as with conventional construction, much of the labor and fabrication for CLT buildings is done at the factory, often using “computer numerical control” (CNC) machines to allow precision cuts.
If provided detailed plans by architects and designers, the factory can fabricate, e.g., a CLT wall exactly to specifications, with door and window openings in the right places and space for plumbing and electric. It virtually eliminates material waste — there are no door and window cutouts to throw away because the wood was never put there in the first place. With computer-guided fabrication, wood is placed only where it is needed.
Because these prefabricated pieces can be assembled a few at a time, in sequence, with relatively little labor, they can be shipped to the construction site on a just-in-time basis, avoiding massive on-site inventory and minimizing on-site disruption. Construction projects can be squeezed into tight, idiosyncratic urban spaces.
Even tall towers can be constructed within weeks, with low labor costs. According to the softwood lumber industry, “Mass timber buildings are roughly 25% faster to construct than concrete buildings and require 90% less construction traffic.”
Factory-based manufacturing “will create a high level of repetition that will blow out the waste and wasted costs” of conventional building, Green says, eventually making something like a kit of parts for house incredibly cheap.
Indeed, in a story for National Geographic, journalist Saul Elbein writes about John Klein, an architect at MIT, who believes “his firm could offer the teeming cities of the 2020s a line of standardized, customizable, mid-rise apartments and office buildings, largely made of modular mass timber, that developers could order to spec like IKEA sofas.”
Right now, Klein says, “every building is a prototype,” designed and built once. Mass timber will help change that.
4. It is fantastic in earthquakes
The performance of mass timber in earthquakes has been much tested (and tested and tested) and has proven remarkably good.
While concrete simply cracks in earthquakes, which means concrete buildings must be demolished and replaced, wood buildings can be repaired after earthquakes.
Mass timber is also lighter and can be built on urban land, e.g. brownfields, not suitable for heavy concrete construction.
5. It is aesthetically and even spiritually appealing
Wood is often left exposed in mass timber buildings — it doesn’t need to be wrapped or bolstered to meet code — and there is nothing quite so beautiful as large expanses of exposed wood. It is appealing on a primal level, a connection to nature. Wood is “nature’s fingerprint in buildings,” as Green puts it, and it has a deeply soothing effect.
Architect Susan Jones of Atelierjones LLC oversaw the building of one of the first CLT single-family residences — her home of five years in Seattle, built to super-efficient passivhaus standards. (It was featured in Dwell Magazine.) “We love living there,” she says. The interior is entirely swathed in timber and “the acoustics are incredibly rich, there’s a beautiful tone, you can still smell a little bit of pine scent in the air, and the way it captures the light is absolute magical.” Jones says, all things considered, building her home with CLT added about 8 percent to total costs.
Mass timber is also a good natural insulator: “Softwood in general has about one-third the thermal insulating ability of a comparable thickness of fiberglass batt insulation, but about 10 times that of concrete and masonry, and 400 times that of solid steel.” That makes it particularly good for windows and doors.
6. It can help pay for good forest management on public land
Forests in the West have become tinderboxes, in part thanks to climate change and in part thanks to years of poor management. They are filled with trees dead or weakened from pine beetle infestations. Decades of overzealous fire protection have left them choked with closely clustered, small-diameter trees. Lately, with all this kindling around, “there’s so much fuel, the intensity of the fire wipes out everything,” says Hilary Franz, commissioner of public lands in Washington state. The land is being permanently scarred.
The forests on public lands badly need thinning, but there’s never enough funding. This has given Franz an idea: use weak and small trees, for which there is no other market, for mass timber. (Logs with tops as small as 4.5 inches will work.) A sufficiently large market for mass timber would create funding for thinning those trees out. As a bonus, Franz wants to use mass timber to build low-cost affordable housing on publicly managed land.
7. It can create jobs in struggling rural areas
Softwood (mostly pine, spruce, or fir) forests in the US are predominantly found in the Northwest and the Southeast, and the communities that live and work in them have been struggling, especially since the housing crash and the great recession.
New demand for softwood could help reopen some of the closed mills and revive some of those communities, aligning their interests with a Green New Deal-style program of national revitalization.
8. There is no other choice
In his TED talk, Green notes that billions of people worldwide lack homes — a half-million in North America — and will need to be housed in the coming century, largely in cities. If all that urban housing is accomplished with concrete and steel, the climate is hosed.
“Over the next 20 years, more than half of new buildings expected to 2060 will be constructed,” reports the United Nations Environment Program (UNEP). “More alarmingly, two-thirds of those additions are expected to occur in countries that do not currently have mandatory building energy codes in place.”
A more sustainable alternative must be found. And wood is the only material sufficiently abundant and renewable to do the job. We’ve got to figure out how to make it work. “We have no choice,” Green told me. “This is the only option.”
In all that I’ve read and among everyone I’ve talked to about mass timber, I have encountered nothing but enthusiasm about its architectural properties. The one exception may be the Build With Strength coalition, which fought mass timber’s inclusion in the IBC, characterizing it as rickety, highly flammable, and environmentally unsustainable. But Build With Strength is, ahem, sponsored by the concrete industry.
By and large, architects and builders are excited about mass timber, as are timber businesses and communities, timber-state politicians, climate hawks concerned about the carbon impact of building, and city officials looking for ways to accelerate decarbonization (and win some good PR).
It hasn’t all been smooth sailing — several CLT panels cracked and collapsed during construction of an Oregon State University building in March 2018; plans for a wooden tower in Portland, Oregon, fell through — but the tailwinds behind mass timber are strong. A material that can be grown in abundance, creates rural jobs, reduces construction waste and labor costs, and slows the growth of concrete and steel seems like a win-win-win.
The good-faith reservations that do exist are about the supply chain, and they come in two forms.
First, protecting and properly managing forests is a huge part of fighting climate change and preserving a livable world. Intact forest ecosystems provide not only carbon sequestration but ecosystem services, wild animal habitat, recreation, and beauty.
Environmentalists worry that North American forests are not sufficiently protected to weather a sharp uptick in demand. The Natural Resources Defense Council has a harrowing report on the (systematically undercounted) amount of GHGs being released by clearcutting in Canada’s boreal forest, as intact ecosystems are replaced by managed forest monocrops. (More on the damage to the boreal in this report.) Oregon Wild has a similar account of that state’s outdated forestry rules, some of the weakest in the nation.
There are two competing certification standards for harvested wood: the Sustainable Forestry Initiative (SFI), sponsored by the industry, and the Forest Stewardship Council (FSC), an independent body created by environmentalists. Unsurprisingly, the FSC standards are considerably more strict regarding clearcutting, pesticide use, and more. Though the SFI has its defenders and has made reforms recently, environmentalists remain unimpressed and several architects and builders I talked to strongly preferred to source FSC wood. (Jones said she suggests it to clients, but it adds a 10 percent premium, so they don’t always go for it.)
Second and relatedly, some environmentalists worry that the sequestration benefits of wood as a building material are being overestimated.
The International Institute for Sustainable Development issued a report last year looking at gaps and weaknesses in lifecycle analysis as applied to building materials, wood in particular. They found that “existing LCAs produce widely variable results, even for similar buildings,” that there is wide regional variability in building performance, and, most notably, that LCA tends to exaggerate the importance of “embodied carbon” in the wood by ignoring or underplaying emissions in other parts of the life cycle.
Specifically, it said, the most uncertain parts of most LCAs have to do with carbon sequestered in wood and carbon released at the end of life — two issues of central importance to mass timber.
Numerous environmental groups, led by the Sierra Club, signed an open letter to California state officials in 2018, urging caution about mass timber. Notably, they did not oppose it outright. They argued that, thanks to current forestry practices, its climate benefits have been exaggerated. “CLT cannot be climate-smart unless it comes from climate-smart forestry,” they said.
The letter provides a short list of principles that should guide climate-smart forestry, including: “Logging of the world’s remaining mature and primary forests, as well as unroaded/undeveloped and other intact forest landscapes, should cease.” And: “Tree plantations should not be established at the expense of natural forests.”
While it is not perfect, they concluded, “FSC certification of privately owned forestlands can support progress in the right direction.”
“There’s no question that [FSC] is the gold standard,” says Jones, “but it’s all better than not doing anything.”
What should we conclude from all this?
There are many ways to reduce the environmental and climate impact of the building sector, some of which are arguably more important, at least for now, than the embodied carbon of materials. They include dense urban infill and multimodal transportation, more sustainable supply chains and construction practices, electrification of heating and cooling, and better building performance (efficient heat, light, and air circulation).
But still, the math is clear: It will be a disaster if we try to accommodate a rising, urbanizing 21st century population with buildings made of concrete and steel, just as it will be a disaster if we try to do it with energy generated from fossil fuels.
Mass timber appears to be the only viable alternative. And it’s cool! It cuts down on waste and costs, opens up the possibility of factory-based mass production of low-cost housing, and has sparked the interest and creativity of the building community. “It’s so much fun!” Jones says.
As cool as it is, though, it would also be a disaster if a turn to mass timber resulted in further loss of mature forests and intensified clearcutting. The impact of unsustainable forestry could undo the rest of the benefits.
To me, the moral, economic, and strategic arguments all point in the same direction: Mass timber is worth celebrating and supporting, but it must always and everywhere go hand-in-hand with a renewed emphasis on climate-smart forestry. At the very least, everyone advocating for or involved in mass timber should be pushing for FSC certification standards to become a regulatory floor, not a voluntary ceiling.
There is enough wood; Green estimates that it takes about 13 minutes for 20 North American forests to collectively grow enough wood for a 20-story building. But if we want the forests to do more for us, to provide all our apartments, offices, and houses, we must care for them so that they can do the same for future generations.
Source: Vox
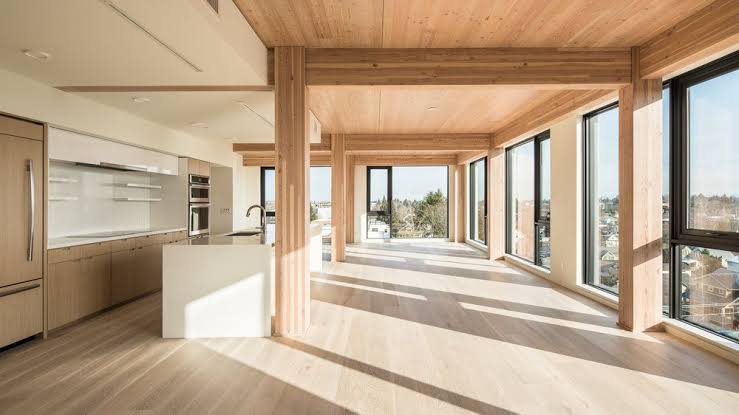
Leave a comment