The Nigerian government’s plan to establish building material manufacturing hubs is seen as a crucial step toward resolving the ongoing crisis in the country’s construction sector.
With the industry heavily dependent on imported materials, experts believe these hubs could drastically cut costs, boost local production, and generate employment.
Ahmed Dangiwa, the minister of housing and urban development, recently announced that the Federal Government will set up these hubs across Nigeria’s six geopolitical zones.
The goal is to lower the cost of building materials and improve housing affordability nationwide.
This initiative also seeks to leverage Nigeria’s abundant natural resources, reduce reliance on foreign exchange, and make construction materials more accessible while promoting sustainability and long-term growth in the sector.
Speaking with BusinessDay Newspapers, John-Bede Anthonio, real estate expert, emphasised the pressing challenges and potential opportunities within Nigeria’s building materials sector.
Having advocated for local production of building materials for over two decades, Anthonio underscored the vital role the domestic industry could play in reducing construction costs and driving economic growth in the country.
According to Anthonio, a staggering 80% of building materials in Nigeria are imported, a situation he believes is unsustainable.
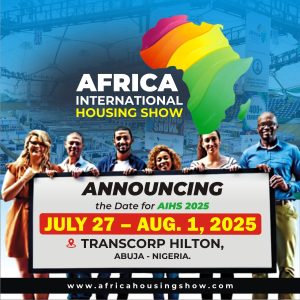
“The only thing that’s not imported is cement, thanks to companies like Dangote and Bua. But everything else, including things like electrical wiring and even wood, is imported, despite the abundance of natural resources like timber in Nigeria,” he noted.
“This dependency on foreign materials, he argued, has been exacerbated by the country’s fluctuating exchange rates, pushing up costs”, he said.
One of the key issues Anthonio highlighted is the role of foreign companies and professionals in the Nigerian building industry.
While local architects and builders struggle with high costs and limited access to resources, foreign architects are increasingly looking to enter the market.
Anthonio believes that Nigeria needs to focus on creating local hubs for building materials production, offering incentives like free land allocations, security, and reliable power supply to attract both local and international investors.
“The government needs to incentivise local production by offering support, such as land allocation and infrastructure development. We also need reliable power and security for these hubs to thrive,” he added.
He believes that establishing such hubs could significantly reduce the cost of building materials and offer a solution to the nation’s growing housing deficit.
“Nigeria needs about 17 million houses, but we’re only building about 200,000 annually. We need to ramp up construction to at least a million units per year,” Anthonio urged.
He advocates for more affordable, smaller units such as one- and two-bedroom apartments, which he believes would cater to the needs of most Nigerians.
Anthonio’s comments align with the need for local building materials that are abundant in Nigeria. Materials like clay, timber, and certain raw materials could be harnessed for local production.
He sees potential in clay, which is readily available and can be used for affordable building solutions.
“If we focus on producing materials like clay locally, we could save on foreign exchange and create more jobs,” he stated.
Anthonio pointed out that the construction sector is the second-largest employer of labour in Nigeria. By increasing local production of building materials, the country could create thousands of jobs, boosting employment and supporting the economy.
“Construction is a major employer. If we can produce materials locally, we will employ many people, which will have a multiplier effect on other sectors,” he explained.
However, he also raised concerns about the government’s ability to execute these plans effectively.
“If the government gets it right, the initiative could be very successful. But historically, ministries have struggled to deliver on such projects. A special independent body should be created to manage this initiative,” Anthonio suggested.
Despite this skepticism, he expressed hope that with the right leadership and a focus on private sector-driven development, the initiative could succeed.
He also underscored the importance of political will in driving the initiative. “If the political will is not there, this will fail,” he said, stressing that government support and the involvement of professionals are crucial to the success of local production hubs.
“The demand for building materials in Nigeria is huge. If we get it right, we can attract foreign investment from countries like Turkey, China, and Malaysia, which have expertise in this area”, he added
The prices of building materials in Nigeria remain variable, reflecting ongoing challenges in the construction sector. Sharp sand, one of the most essential materials, is priced between ₦42,000 and ₦45,000 per 20-ton load, while filling sand costs between ₦30,000 and ₦32,000 per 10 tons. Black soil filling sand, a common alternative, is available for ₦19,000 to ₦21,000 for 10 tonnes.
For larger-scale construction projects, the cost of boulders varies widely depending on size.
Small boulders, weighing 15 tonnes, are priced between ₦50,000 and ₦55,000, while large boulders can range from ₦70,000 to as much as ₦175,000 for the same quantity.
Steel rods, crucial for reinforcement, are priced according to their size. An 8 mm rod can cost between ₦700 and ₦1,050 per piece, while a 10 mm rod ranges from ₦1,000 to ₦4,100 per length. Larger rods like the 12 mm and 16 mm are priced between ₦1,100 and ₦4,500, and ₦1,500 to ₦5,000 per piece, respectively. The cost for the 25 mm rod is higher, ranging from ₦4,500 to ₦7,800 per piece.
In addition to steel rods, BRC Mesh, commonly used for reinforcement in concrete works, is priced between ₦14,000 and ₦18,000 for a 20-meter roll of 3.5 mm mesh.
These fluctuating prices highlight the ongoing challenges faced by builders and developers in Nigeria, particularly in light of the economic pressures from inflation and exchange rate volatility.
Despite the availability of local resources, reliance on imported materials and rising costs continue to impact the affordability of construction projects across the country.
On his part, Salisu Haiba, the Director of Press and Public Relations at the Ministry of Housing and Urban Development, echoed Anthonio’s sentiments about the potential of local materials.
He highlighted that materials like stone, earth, wood, bamboo, and plant-based materials are often abundant and cost-effective.
“Local materials can be sourced from the immediate environment. These materials are often readily available and can reduce construction costs significantly,” Haiba explained.
The Nigerian government is also working towards creating local production hubs to reduce dependence on imports.
Haiba mentioned that two investors have already expressed interest in the initiative, and the Infrastructure Concession Regulatory Commission (ICRC) is overseeing the process to ensure the partnership moves forward. “Each area has its own unique materials in abundance.
Investors will harness what’s available in their respective environments to meet the needs of the local market,” he added.
Anthonio and Haiba are optimistic about the future of Nigeria’s building materials industry, provided the government and private sector can collaborate effectively.
The creation of local production hubs could be a game-changer, not only for the construction sector but for the Nigerian economy as a whole, offering a path toward sustainable development, job creation, and reduced reliance on expensive imports.