Dirty, To Be Concrete
Concrete is the most used human-made material. Cement, its binding agent, makes up just 10-15 percent of its mass but accounts for most of its carbon emissions, due to chemical reactions during the energy-intensive manufacturing process. Cement is a top source of emissions, accounting for around eight percent of global carbon emissions. Decarbonizing construction is critical to meeting Paris Agreement obligations. But unlike other essential, high-emissions sectors such as heating, electricity, and transport – which can be abated with heat pumps, renewables and nuclear, and batteries – there is no obvious low-emissions replacement for the most ubiquitous construction material.
Incorporating carbon capture, utilization, and storage (CCUS) technologies into the manufacturing process presents a promising opportunity for this sector to go green. Although CCUS has a limited commercial presence, a recent report of the International Energy Forum identifies the technology as the missing link between energy security, affordability, and decarbonization goals and highlights strategies for deployment to leap forward. Harnessing captured CO2 in concrete can complement nature inclusive building techniques. Turning emissions to value by combining engineered and nature-based solutions in construction also offers a viable alternative to underground storage.
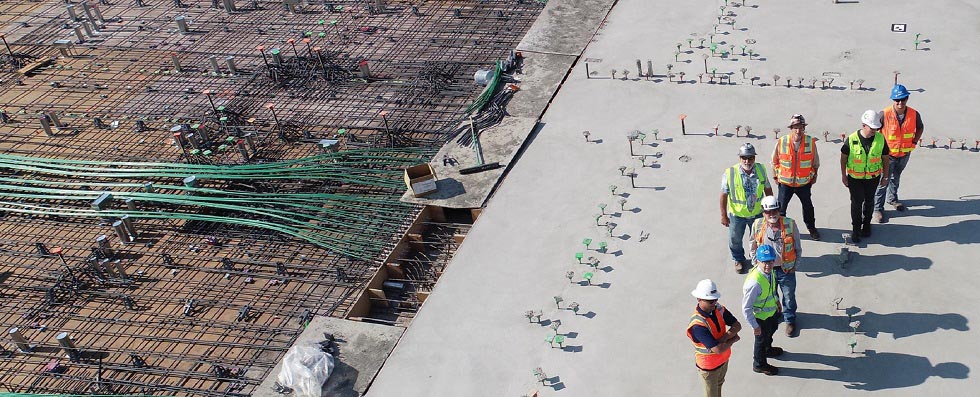
Concrete from CO2
There are various pathways by which CO2 is converted into solid carbonatesto augment or substitute concrete ingredients. It can be injected to cure the cement mix (replacing energy-intensive steam curing) and mineralizing to strengthen the concrete; it can react with calcium or magnesium oxide to form a solid carbonate, substituting or augmenting aggregates and other concrete components; and it can be used as an input for a CO2-based, non-cementitious concrete.
All these approaches involve the concrete locking away the carbon for good, unless it is burned. This is a particularly attractive CCUS application, as other uses of captured carbon may return the carbon to the atmosphere over time. If scaled up sufficiently, CO2-infused concrete could eventually serve as a carbon sink. A report from Carbon 180 concludes: “New and emerging technologies enable CCUS across nearly every major concrete component. At scale, these solutions can one day lead to carbon-negative concrete, the point at which more emissions are captured and stored in the material than are generated in its production and use.”
Although injecting captured CO2 into concrete is not equivalent to actively removing it from the atmosphere, it provides an opportunity for a high-emissions sector to offset emissions while stimulating a potential market for captured CO2.
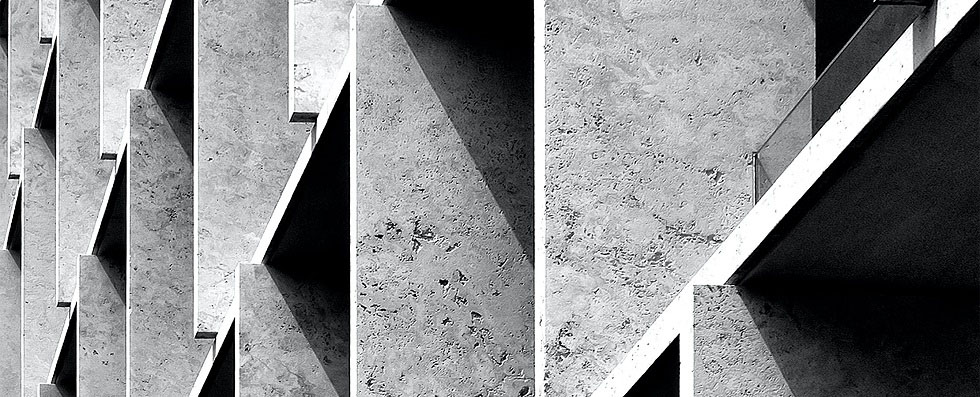
Commercializing CO2-to-concrete
Technologies for incorporating captured carbon in concrete occupy a small corner of the vast construction industry, but it is attracting considerable interest. Halifax-based CarbonCure Technologies, which offers a carbon mineralization method for ready-mix and precast concrete, has received support from investors including Microsoft and Amazon (the latter plans to use CarbonCure products for its new Virginia headquarters).
Dozens of other start-ups offer their own approaches to the problem. New Jersey-based Solidia uses carbon instead of water to cure low-lime cement, cutting carbon up to 70 per cent. London-based Carbon8 Systems has developed technology that is installed at cement plants to capture CO2 and cure bypass dust (a by-product) to create ‘carbon-negative aggregate’.
Montreal-based Carbicrete, meanwhile, says it can produce ‘cement-free, carbon-negative concrete‘. Cement is normally made by heating calcium carbonate to nearly 1,500°C to extract calcium oxide, consuming huge amounts of energy and emitting CO2 in the process. However, Carbicrete avoids these emissions by combining captured CO2 from industrial sites with waste slag from steelmakers, which contains calcium oxide. During the 24-hour carbonation process – which requires no heating – CO2 is converted into stable calcium carbonates, filling voids to form a dense structure which strengthens the concrete. The resulting carbonated concrete has up to 30 percent higher compressive strength than conventional concrete.
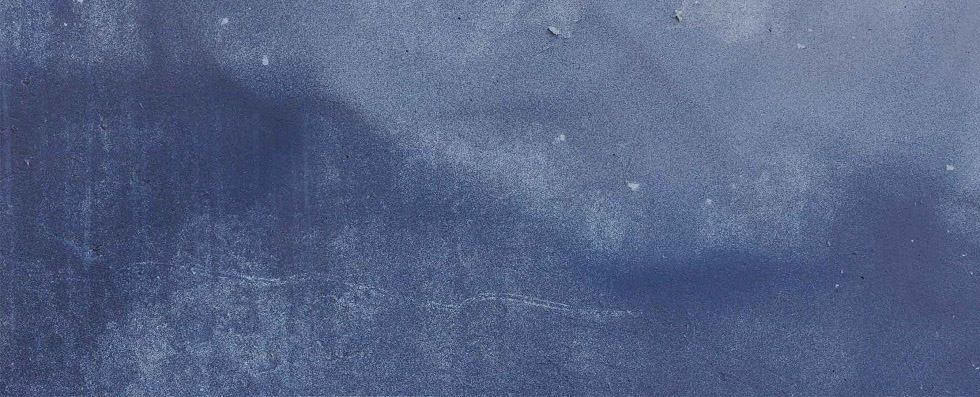
At present Carbicrete’s carbon curing process can only be carried out in a carefully controlled environment, restricting its use to products cast in advance of delivery to a construction site, and excluding use from liquid ready-mix concrete.
Although there are obstacles to scaling up these technologies, for an industry with such large and hard-to-abate emissions, each of these companies’ offerings presents possibilities. UK Concrete estimates that CCUS could deliver 61 percent of the carbon savingsthe concrete industry needs to make to become net carbon negative by 2050.
source: ief