‘Habitat for Humanity‘ is well-known for helping people achieve their dream of owning a home. With 3D-printing technology, it’s making homeownership even more affordable.
Since its inception in 1976, Habitat for Humanity has built hundreds of thousands of affordable houses for those in need. Habitat for Humanity just finished its first 3D-printed house in Williamsburg, Virginia, utilizing automated computer technology and a unique concrete mix. April Stringfield, the house’s new owner, and her 13-year-old son are eager to move in and make the place their home.
While 3D-printed buildings are still uncommon, the Williamsburg house’s successful completion demonstrates the growing desire to build affordable homes while protecting natural resources like trees.
The Williamsburg house is still a typical house, despite the fact that the walls are printed rather than stick-framed. It has three bedrooms, two full bathrooms, and a covered front porch where Stringfield may spend sunny summer evenings in 1,200 square feet of living space.
Traditional siding was employed on the roof gables, and regular bricks were used on the porch pillars. Stringfield also received a 3D printer, which she will use to build cabinet hardware and light switch covers in addition to the house.
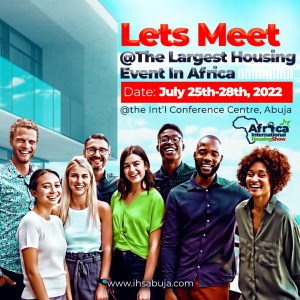
During the pandemic, some building material prices doubled or tripled primarily due to supply chain issues, which subsequently drove up homebuilding costs. By using concrete rather than wood, Alquist, the contractor that printed the walls of Stringfield’s new home saved Habitat an estimated 15 percent per square foot.
While homebuyers do not pay for the labor needed to construct a Habitat home, they do pay for the cost of construction materials. In this way, the money saved on material costs is passed on directly to the buyer.
It took just 28 hours to print the concrete walls of Stringfield’s home. Alquist uses a patented concrete mix and impressive-looking extrusion machine to print exterior and interior walls, which are reinforced with steel during the printing process.
Afterward, the exterior walls are sealed with a clear or tinted coating that keeps moisture from transferring through the concrete. Homeowners can choose a standard gray concrete color or select from a range of attractive earth tone hues to give the home a custom look.
After Alquist finished printing the walls, traditional builders constructed the roof, ran plumbing and wiring, and installed interior flooring and other finishes. Through the Williamsburg chapter of Habitat, contractors, subcontractors, and other volunteers donated their time to complete the remaining parts of the house.
As a Habitat rule, new homeowners must spend some of their own time working on the project, so Stringfield put in 300 hours of sweat equity to make her new home a reality.
While the Williamsburg house is the first 3D-printed home Habitat has completed, it likely won’t be the last. The Habitat buyer program exists to help encourage homeownership for those who need housing but might not be able to purchase a home through conventional means.
Successful Habitat home applicants commit to working on the project or at a Habitat ReStore, and they learn how to budget for mortgage payments and care for their new home. The nationwide nonprofit does not discriminate when selecting homebuyers.
The Future of 3D Construction
Home-based automated 3D printing is still in its infancy. Computer-constructed homes, such as this 3D-printed house in Riverhead, New York, are already being created and sold to the general public. Standard construction, on the other hand, is still the name of the game in most communities and will likely remain so for the foreseeable future.
Stringfield is ecstatic about her new home, telling CNN that she is grateful to have a backyard where her son can play and her puppy can run.