Low-carbon brick industry clusters present a strong model to create local supply chains necessary to address the high demand for affordable housing in Africa’s Great Lakes region while decreasing foreign imports. Fatou Dieye and Daniel Wyss outline a true model for green industrialisation.
Like many African cities whose limited resources are strained by the pressures of rapid urban transformation, the cities in the Great Lakes Region (Rwanda, Burundi and Eastern DRC) suffer from the typical signs of construction industry dysfunction: large quantities and high costs of imported building materials and a shortage of local construction firms with access to the skilled labour and financing required for building standardised housing at mass scale.
Consequently, despite a handful of well-planned housing schemes, the construction of informal housing persists and low-income households continue to cluster in fire, flood and earthquake-prone settlements.
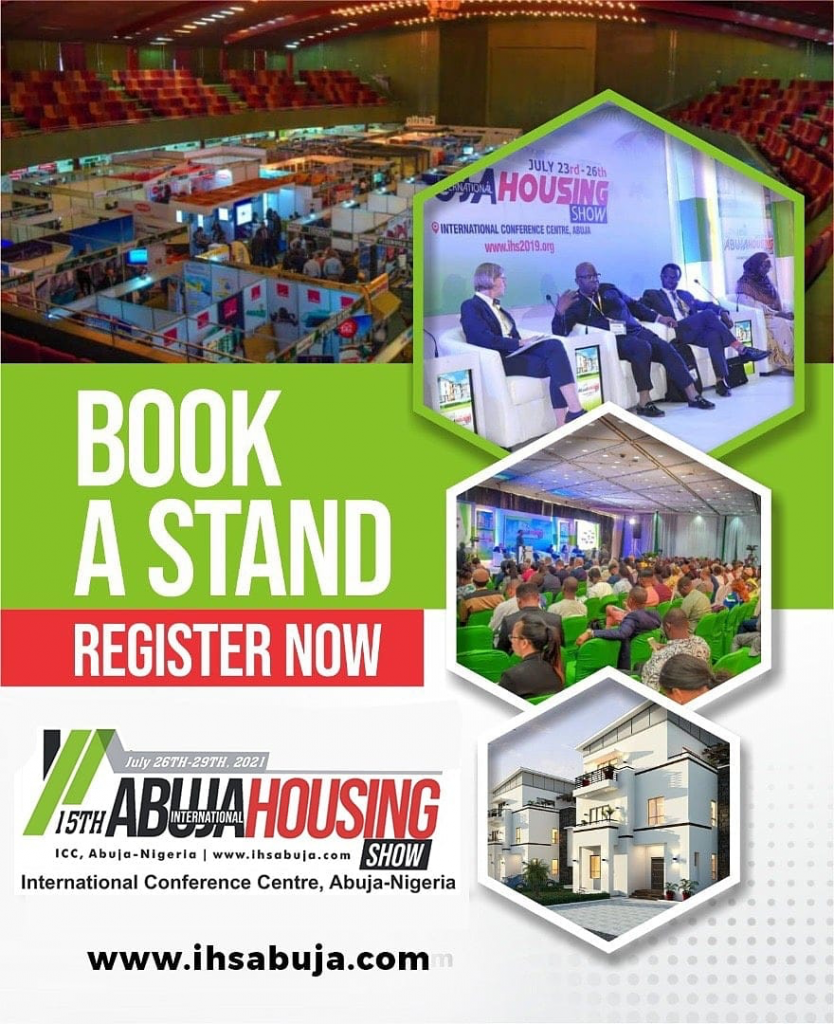
With one new dwelling unit built every five minutes, the economic and environmental consequences of this dynamic are crippling: millions of trees are cut illegally every year for the informal production of substandard bricks and the construction market exists in near-total dependence on foreign cement, further draining capital from the local economy.
Skat Consulting Ltd., a Swiss team of building technology and construction sector experts, first offered its expertise to the Rwandan construction industry in the early 1980s. Since 2012, Skat has served as the implementation agency for the PROECCO Project (promoting employment through climate responsive construction), aimed at stimulating green and inclusive urban development in Africa’s Great Lakes, and supported by the Swiss Agency for Development and Cooperation (SDC).
In 2018, Skat demonstrated its partner-driven approach to strengthening and greening local supply chains for housing delivery and the participatory upgrading of informal settlements. This is done via the design, construction and demonstration of an Affordable Urban Housing System for incremental transformation of unplanned neighbourhoods.
Located along the Mpazi channel in one of Kigali’s densest and most popular informal settlements, the Mpazi project brought together local authorities, homeowners, builders and engineers to perform a land consolidation and construction exercise to transform an existing group of substandard mud brick houses into a built-to-code condominium.
Made of modern bricks from local makers using energy-efficient technologies and CO2 neutral fuels, the project forged a direct link between local building material producers and builders.
This was a job-creation strategy, designed to both test the feasibility of redirecting capital from an active construction industry towards local brick makers, as well as to demonstrate the possibility of reducing the climate impact of industrialisation and
urban expansion.
By designing solutions that address the unmet demand for affordable housing and the pressing need for off-farm jobs, Skat’s inclusive approach effectively unlocks barriers for all partners along the housing supply chain.
Direct collaboration
For local authorities, PROECCO provided a platform for direct collaboration with landowners, eliminating the need for costly expropriation exercises and ensuring conformity with master plan regulations.
For home-owners, the new modern brick building technologies and house designs promoted by Skat respected the income profiles typical of most unplanned neighbourhoods, all while offering the opportunity to serve as collateral for future business credits – an attractive proposal for banks looking to design, standardise and finance housing credit products.
Since the inauguration of the Affordable Urban Housing Demonstration Block, the technologies promoted by Skat have been replicated more than 2,000 times. This an important sign that the local private sector has begun to establish the key supply partnerships – between builders, brick makers, raw material suppliers and the other service providers – which are needed to deliver affordable modern brick building solutions at mass scale. This can also meet urban building regulations and the CO2 Certificates’ Gold Standard.
In partnership with SDC, Skat will continue to facilitate this industry transformation and upscaling process through 2025, primarily through the design of low-carbon brick industry clusters and centralised building material production hubs capable of feeding the region’s hungry construction markets.
While many external pressures may cause businesses to cluster in shared locations, the brick industry is one of the most obvious examples of natural clustering behaviour as brick producers settle near their primary material resource: clay valleys.
With its nearly inexhaustible quantities of high-quality clay, the low-carbon brick industry clusters present a strong model for the Great Lakes to create the local supply chains necessary to address the high demand for affordable housing while decreasing foreign imports.
Furthermore, the economic benefits of the cluster are closely tied to its environmental ones, making it a true model for green industrialisation in one of the world’s fastest urbanising hotspots.
Fatou Dieye is Skat’s country representative in Rwanda. Daniel Wyss is Architect and Urban Development and Construction Industry Specialist for the company.
Source: Nairametrics